News
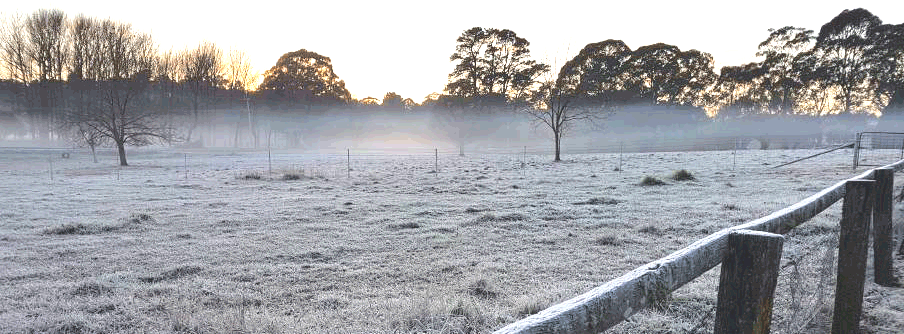
Cold Weather Precautions
April 29, 2021
With the onset of the cold, damp and often dark conditions of the southern hemisphere’s winter months many manufacturers are readying themselves for an inevitable increase in calls from contractors and home DIY’ers alike.
The calls usually start along the lines “Ive used your product on our project and it just doesn’t work, there is something wrong with it! *!%* insert expletive here *%!*”. While we completely understand the frustration in lost time and productivity, most often the issues arise from the environmental conditions at the time of application, not the product or installer.
Lets take this opportunity, ahead of time, to investigate the issues and available solutions together:
Tile Adhesives and Floor levelling
Cementitous products (most powdered material) utilise chemical reactions to cure and set. Like most chemical reactions, as temperatures drop, the reactivity of cement slows considerably. At temperatures much below 0oc the reaction can stop completely and the product may not set at all. It is important to consider the products open (set) time and expected temperatures when preparing to lay a floor. Try and work at ambient temperatures above 10oc only.
Mastic or other water based tile adhesives (most ready to use pastes) cure by a process of through drying. The water leaves the system through evaporation into the atmosphere around the newly laid adhesive. As temperatures drop, the rate of evaporation slows and set times extend substantially. As a further complication, because these products contain water they are at risk of partially freezing. Not only does this make them thick and difficult to use at low temperatures, it can irrevocably damage the delicate polymer suspensions, rendering the product unusable.
Tile Grout
A considerable amount of cementitious adhesive technology is shared with floor and wall tile grout products. They too rely on chemical reactions to dry and as such can suffer all of the same issues their adhesive counterparts do as temperatures plunge.
Because these products are visible to the client once the job is finished this is often where efflorescence rears its ugly head, customers hate it… Efflorescence generally describes the crusty white deposit visible on a masonry surface. It becomes more of an issue in colder climbs as it is caused by the carbonation of alkaline salts present in the chemical reaction as they react with atmospheric carbon dioxide and water to form calcium carbonate. At colder temperatures the slowed transience of reaction moisture allows more time for these chemicals to be carried to the surface as the water evaporates out of the system. Premature treatment or sealing for efflorescence usually only exacerbates the problem. We will talk more about efflorescence in a later newsletter.
Epoxy Systems
Epoxy based adhesives, grouts and sealers are thermosetting polymers that typically employ a resin and a hardener component. When mixed together at a recommended ratio the resultant chemical reaction provides the unique mechanical and resistance properties of a given product. Not only do cold temperatures thicken both components making it virtually impossible to mix effectively, they also slow or halt the chemical reaction lengthening set times considerably. Evaporation rates also play a role in solvent or water based products as it simply takes longer for the carrier to leave the system.
Regardless of the chosen technology, almost all Technical Data Sheets utilise laboratory testing temperatures (~22oc) to quote working and set times. Without qualifying the resulting strengths of a specific material, should a product’s TDS state a set time of ~6hrs at 22oc it will likely be double that at 10oc and more than 20hrs at 0oc.
- Always read, understand and follow the manufacturers instructions for each product to be used.
- Use environmental controls to keep the working environment above 10oc while products are setting.
- Where possible use rapid setting products to reduce cure times.
- Pay close attention to recommended water levels and only use the minimum required to reach a workable consistency.
- Allow for additional drying times between each step of your job.
- Increase ventilation for additional evaporation across the worksite.
- Remember that night time temps can be significantly lower than the day, get your work done before lunch to allow them time to cure before the day cools off.
- Unless advised by the manufacturer, never add accelerators or hot water to cement systems in an attempt to reduce set times.
- Store products outside or where the temperature could drop below zero, always condition your materials before starting a job.
- Get caught out with poor organisation and work in the coldest part of the day.
- Work in an uncontrolled environment when the temperature is likely to be much below 10oc, below 5oc necessitates meticulous planning.
- Use forced air heating across your worksite as this often causes premature surface drying and results in damage and cracking.
- If working outside, consider the weather and delay work if rain or cold weather is forecast.