Its Silver! EcoVadis
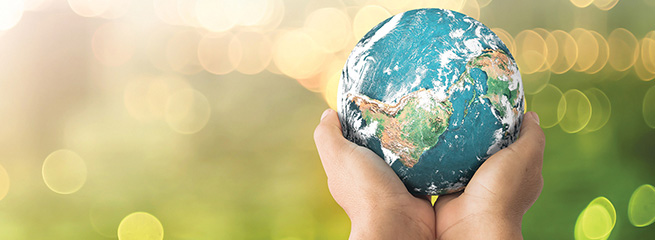
Its Silver! EcoVadis
January 8, 2022
Adjuvate has recently been awarded a prestigious silver classification by EcoVadis for our commitment to Corporate Social Responsibility.
We are proud that this recognition places us within the top 25% of the world’s best companies as assessed by EcoVadis.
EcoVadis is one of the most recognised and trusted providers of business sustainability ratings throughout industry. Such high praise is especially valuable for Adjuvate, given that this was our first formal evaluation and we achieved a classification normally reserved only for much larger multinational corporations.
EcoVadis ranks Adjuvate among the world’s best companies participating in the mutually beneficial assessment. Quite an arduous task, the very thorough evaluation individually assesses applicant companies on their Environmental Response, Labour and Human Rights, Ethics, and Sustainable Procurement.
With the growing importance of sustainability in making business decisions, the high classification achieved through independent assessment is not only recognition of our commitment to sustainable and responsible behaviour, but a credible message to the global market that Adjuvate is serious about CSR and partnering with like minded corporations from around the world.
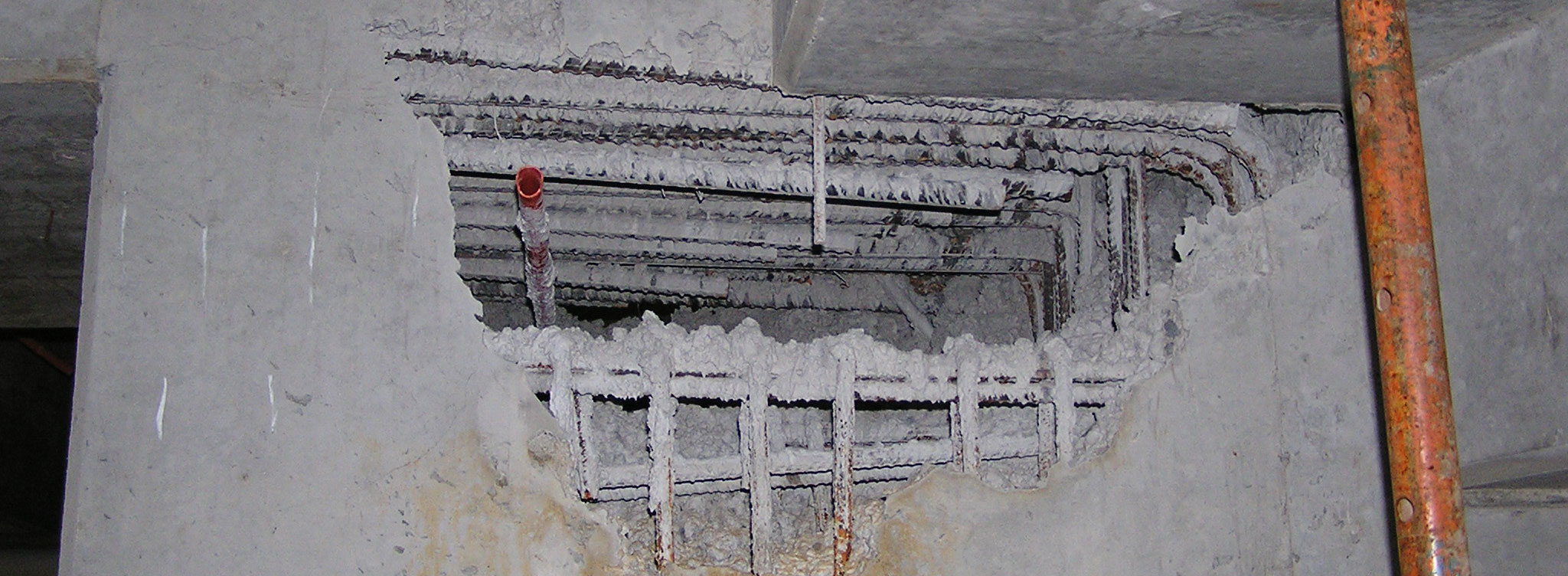
Understanding Construction Grouts
July 25, 2021
Whilst construction grouts are common on many construction sites, the technologies behind them and their typical applications are often shrouded in “brand name” mystique. Here we aim to provide a little better understanding of the basic materials and each’s versatility on-site, helping to demystify the product ranges and make it easier to apply the best product to your next job.
Adjuvate has almost 30 years direct experience in the development, manufacture and supply of a range of specialty construction grouts. Our strong toll manufacturing relationships have seen us produce well over 1,000T a year of numerous products for more than a decade. The Adjuvate ConGrout range of construction grouts have a long performance history having been specified heavily throughout Australia, the Pacific and Asia.
There is a general industry misconception that construction grouts require specialist equipment and must only be installed by product experts. Whilst there are applications that could require specific knowledge or equipment, for the majority of situations a general contractor is more than capable of following the few basic principles that lead to application success!
Construction Grout’s, what are they?
As a general description, cemetitous construction grouts are cement and aggregate blends that have been modified, in one way or another, to provide specific characteristics designed to enhance their use in differing construction applications.
More highly engineered construction grouts require modification/s to overcome workability, ultimate strength and shrinkage shortcomings inherent of more basic grouts.
As designers of specific grouting systems we employ numerous combinations of modification technologies to achieve the required product characteristics.
These can include:
- Specialist cement products
- Close grading of selective aggregate sizing
- Specialised inert fillers
- Pozzolan addition (Fly Ash, Silica Fume, Blast Furnace Slag)
- Set accelerators or retarders
- Hydration modifiers
- Shrinkage compensation or expansion additives
When the manufacturer’s directions are followed and water is added to the product a series of one-way chemical reactions are initiated that result in the required final properties of the grout.
Firstly, the hydration modifiers (superplasticisers) disperse throughout the mix, fluidising the product and rapidly ensuring that all parts of the mixture receive the water required to initiate the further reactions.
The water encourages the cement to react with the various minerals within the formulation, often referred to as pozzolans, causing them to link with the cement and sand aggregate particles.
Any retarding systems will then initiate as the cement and other ingredients inter-react to start forming crystalline structures. These systems are designed to overcome and slow the cement’s chemical reaction and provide for a longer working time.
At the same time reactions start to minutely grow the slowly hardening cement matrix while still in the wet ‘plastic’ stage. Shrinkage compensation or expansion aids promote growth to positively increase volume or offset the shrinkage that occurs with conventional mortar or concrete.
As the crystal growth continues and final set is achieved the compressive strength of the system begins to increase until final measurements can be achieved at 28 days.
Engineered construction grouts are generally classified by the method utilised to provide expansion or offset plastic shrinkage. Cementitous grouts will generally fall within 5 types or classes. We will concentrate below on Class’s A and C being by far the most commonly used;
Class A
These products expand through the formation of a micropore gas that is a result of the reaction of the cement componentry and a very small quantity of a metal oxide or refined mineral.
Often referred to as GP Grout, this class is the most commonly found on construction sites and is user friendly, versatile and economical.
Class A grouts are not typically suitable for long distance pumping and the formed micro gas agglomerates to form larger bubbles which weaken the final placement.
Adjuvate ConGrout A includes additional materials designed to promote secondary crystal growth in setting grout. Average total expansion is shown to be in excess of 3%.
Class C
These systems utilise additions that create expansion through growing crystals within the setting phase of the grout and beyond. The growth rate of these crystals is engineered to neutralise the natural shrinkage of more standard concrete formulations. Class C grouts commonly employ minimal expansion aids which result in negligible shrinkage when compared to standard mortar and concrete. Class C grouts are sometimes referred to as limited shrinkage grouts.
More suited to pumping applications and often formulated as a dual Class C-A grout to reap the benefit of both technologies.
Adjuvate ConGrout C is engineered as a neutral expansion grout in that it exhibits net zero growth or shrinkage once cured.
How to use construction Grouts
Always wear appropriate PPE and be sure to read, understand and follow the manufacturer’s instructions for the specific product being used.
Careful consideration has been completed by the manufacturer as to water requirement, mix, working and set times to ensure the product complies with specifications and expected characteristics.
It is always a best practice to mix whole containers of product, ideally with a slow speed power mixer and suitable paddle. Grout mixers are also available when larger quantities of grout need to be placed at one time.
Using clean water, add the correct volume to a clean mixing vessel, slowly add approximately half to three quarters of the powder whilst mixing,mix until virtually lump free. Add the remaining powder and mix for the remaining time nominated by the manufacturer.
Thorough mixing is required to ensure that all of the reactive ingredients are effectively dispersed in the grout.
Place the mixed material immediately by pouring, trowel or pump etc. Work into place before the product starts to harden.
Grouting Do’s
- Ensure the application area is clean and free from all contaminants.
- Scabble aged or dirty substrates to improve adhesion of new material.
- Pre-wet substrates but do not leaving standing water.
- Install form boards or shutters as required to ensure full constraint and fill.
- Ensure that the installed grout is appropriately cured to allow hydration and full strength development. Water, builders plastic or a curing compound such as Adcure A should be employed for at least 24hrs.
Grouting Dont’s
- Don’t over water material beyond manufacturer’s recommendation.
- Don’t add more water to hardening grout in an attempt to re-energise it.
- Don’t attempt to accelerate, retard or modify the mixture without manufacturers advice.
- Don’t install cementitous grouts in temperatures below 7°c or above 35°c.
- Don’t install grout in direct contact with aluminium as it can result in galvanic corrosion.
- Never use dirty or salt water.
Confidently install construction grouts, being sure to follow manufacture’s instruction and industry guidelines in the following applications:
- Repair damaged or incorrectly poured concrete
- Under machine base plates or bearing beds
- To support portal framing or non-aluminium or copper pipe and posts
- To infill wall or floor chasings
- Slab dowling, as specified
- Tilt slab joint interfaces that do not require expansion jointing
- Balustrade posts etc
For further information or assistance with specifying please contact our customer service team.
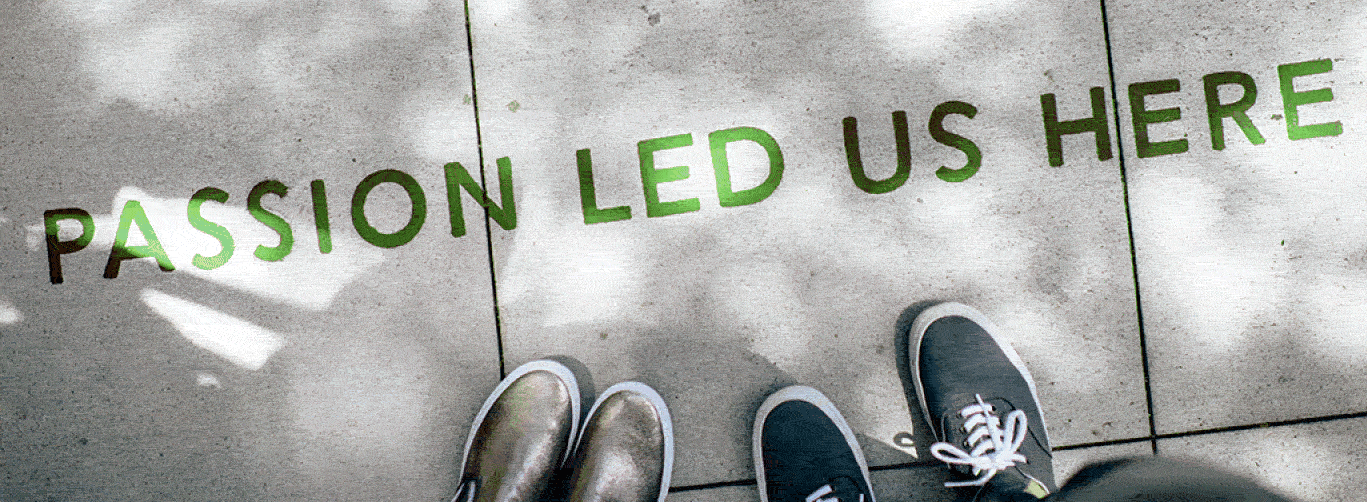
Branding Update
May 21, 2021
Important news! Change is afoot at P. O’Brien and Associates…
After 28 years as a leader in the niche construction chemical industry we are making the move to transition all customers to our world recognised brand name Adjuvate.
Whilst both the P. O’Brien & Associates and Adjuvate names have been around since our 1993 inception, we feel that our Adjuvate branding has now come to better represent our business and people as they have evolved over time.
Please rest assured that this is a change in name only. The same quality, service and absolute commitment to excellence, that you have come to know and trust, will continue long into the future.
During the months to come you will notice changes to our correspondence, packaging and promotional material in line with this exciting announcement.
All company addresses, contacts and banking details will remain unchanged except for the banking account name.
Should you have any questions regarding the planned changes our customer service team would be only too happy to assist.
We look forward to working together as we move forward into this new phase of our business.
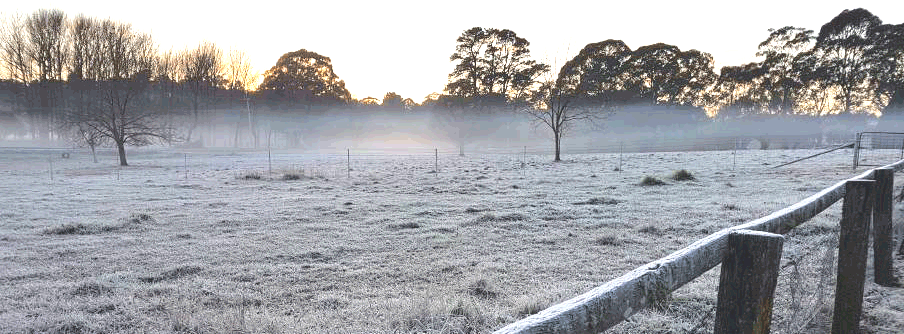
Cold Weather Precautions
April 29, 2021
With the onset of the cold, damp and often dark conditions of the southern hemisphere’s winter months many manufacturers are readying themselves for an inevitable increase in calls from contractors and home DIY’ers alike.
The calls usually start along the lines “Ive used your product on our project and it just doesn’t work, there is something wrong with it! *!%* insert expletive here *%!*”. While we completely understand the frustration in lost time and productivity, most often the issues arise from the environmental conditions at the time of application, not the product or installer.
Lets take this opportunity, ahead of time, to investigate the issues and available solutions together:
Tile Adhesives and Floor levelling
Cementitous products (most powdered material) utilise chemical reactions to cure and set. Like most chemical reactions, as temperatures drop, the reactivity of cement slows considerably. At temperatures much below 0oc the reaction can stop completely and the product may not set at all. It is important to consider the products open (set) time and expected temperatures when preparing to lay a floor. Try and work at ambient temperatures above 10oc only.
Mastic or other water based tile adhesives (most ready to use pastes) cure by a process of through drying. The water leaves the system through evaporation into the atmosphere around the newly laid adhesive. As temperatures drop, the rate of evaporation slows and set times extend substantially. As a further complication, because these products contain water they are at risk of partially freezing. Not only does this make them thick and difficult to use at low temperatures, it can irrevocably damage the delicate polymer suspensions, rendering the product unusable.
Tile Grout
A considerable amount of cementitious adhesive technology is shared with floor and wall tile grout products. They too rely on chemical reactions to dry and as such can suffer all of the same issues their adhesive counterparts do as temperatures plunge.
Because these products are visible to the client once the job is finished this is often where efflorescence rears its ugly head, customers hate it… Efflorescence generally describes the crusty white deposit visible on a masonry surface. It becomes more of an issue in colder climbs as it is caused by the carbonation of alkaline salts present in the chemical reaction as they react with atmospheric carbon dioxide and water to form calcium carbonate. At colder temperatures the slowed transience of reaction moisture allows more time for these chemicals to be carried to the surface as the water evaporates out of the system. Premature treatment or sealing for efflorescence usually only exacerbates the problem. We will talk more about efflorescence in a later newsletter.
Epoxy Systems
Epoxy based adhesives, grouts and sealers are thermosetting polymers that typically employ a resin and a hardener component. When mixed together at a recommended ratio the resultant chemical reaction provides the unique mechanical and resistance properties of a given product. Not only do cold temperatures thicken both components making it virtually impossible to mix effectively, they also slow or halt the chemical reaction lengthening set times considerably. Evaporation rates also play a role in solvent or water based products as it simply takes longer for the carrier to leave the system.
Regardless of the chosen technology, almost all Technical Data Sheets utilise laboratory testing temperatures (~22oc) to quote working and set times. Without qualifying the resulting strengths of a specific material, should a product’s TDS state a set time of ~6hrs at 22oc it will likely be double that at 10oc and more than 20hrs at 0oc.
- Always read, understand and follow the manufacturers instructions for each product to be used.
- Use environmental controls to keep the working environment above 10oc while products are setting.
- Where possible use rapid setting products to reduce cure times.
- Pay close attention to recommended water levels and only use the minimum required to reach a workable consistency.
- Allow for additional drying times between each step of your job.
- Increase ventilation for additional evaporation across the worksite.
- Remember that night time temps can be significantly lower than the day, get your work done before lunch to allow them time to cure before the day cools off.
- Unless advised by the manufacturer, never add accelerators or hot water to cement systems in an attempt to reduce set times.
- Store products outside or where the temperature could drop below zero, always condition your materials before starting a job.
- Get caught out with poor organisation and work in the coldest part of the day.
- Work in an uncontrolled environment when the temperature is likely to be much below 10oc, below 5oc necessitates meticulous planning.
- Use forced air heating across your worksite as this often causes premature surface drying and results in damage and cracking.
- If working outside, consider the weather and delay work if rain or cold weather is forecast.

Sealers & Solvents from Adjuvate
March 29, 2021
Adjuvate Australia is a great place to source high-quality, all-purpose solvents and sealers to be utilised in numerous building applications. All products are formulated in compliance with the most stringent Australian building standards and are perfect for new construction and renovations alike.
Adjuvate’s range of sealers and solvents are available for retail, wholesale and or brand labelled distribution.
Some of the Adjuvate range to consider for your next project;
- Adjuvate Adcure A – An acrylic modified co-polymer concrete curing compound tested to comply with ASTM 3799. Stable, clear and quick-drying the emulsion cures, seals and hardens the the surface of new concrete. Adcure A prevents fresh concrete from drying out during the critical early stages of curing.
- Adjuvate Adcure PVA – A co-polymer curing compound that retards the loss of moisture from fresh concrete during drying. ensuring optimum strength and durability.
- Adjuvate Sealer GP – A Clear Solvent based acrylic penetrating concrete sealer. When correctly applied the system exhibits high adhesion, water resistance and superior durability.
- Adjuvate Saniseal – An acrylic-modified copolymer emulsion designed to prevent bio-contamination and water-dispersible liquids from penetrating new and existing concrete surfaces.
- Adjuvate Sealer RC – Silicone based, Sealer RC is a water-repellent coating made to protect the natural colour and finish of above-ground interior and exterior masonry surfaces.
- Adjuvate GPSOL – A strong aromatic solvent specifically formulated to clean and thin the Adjuvate GP Range of concrete sealers. In most instances the product will re-solvate other coatings and can be used to clean application equipment before the sealer dries.
- Retail Solvents
Browse the complete range at www.adjuvate.com.au today!
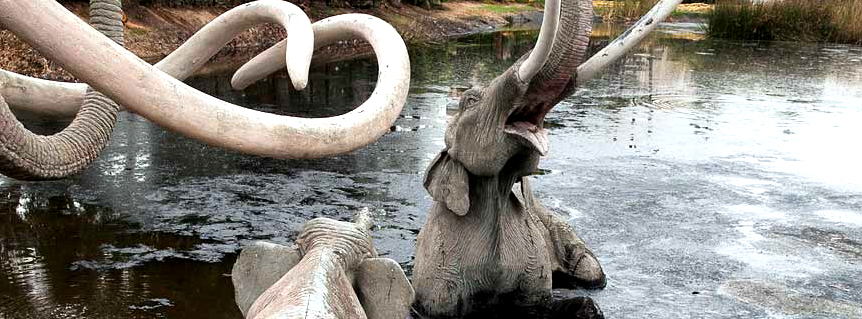
Understanding Bitumen
March 3, 2021
Bitumen like coatings are some of the oldest known products utilised in waterproofing, sealing and protecting structures.
Ancient Egyptians used bitumen like resins to embalm their dead. Centuries later the Vikings would use plant fibres soaked in bitumen to seal their wooden ships. Often these bitumen “ropes” are the main evidence left when Viking wrecks are discovered.
What is Bitumen?
Bitumen occurs naturally in some parts of the world as a thick oily substance found submerged in lakes and often called tar pits. Most famously, the La Brea tar pit in California has provided some of the best preserved prehistoric fossils found to date.
The bitumen we use today is a more consistent manufactured product derived from crude oil. Formed millions of years ago this oil is extracted from vast underground resources that can be discovered either below ground or the sea floor.
Once recovered, the oil is refined through a process of heat to separate it into the many and varied products; Butane, Propane, Petrol, Diesel and then at even higher temperatures, Oils and Waxes.
The final product rendered is the sticky black material we now call bitumen.
Tar and Bitumen, aren’t they the same thing?
No! Tar is produced from coal, not oil like Bitumen. While coal was originally formed from plant material under the earths pressure, it is considered highly toxic as a processed material.
Coal Tar, creosote, pitch, moth balls and various other resins come from tar derived of coal.
Advantages of Bitumen
Cost effective when compared to synthetic materials
Highly water resistant, in fact impervious to water
Exhibits great adhesion properties
The only real shortcoming of bitumen is that over relatively long periods of exposure to sunlight (UV) it tends to break down, harden and become brittle.
Adjuvate Australia has long recognised the specific performance benefits of bitumen based products and has developed a range of products to meet most applications.
BlakJak
The thickest consistency, often called knife grade as it is installed with a putty knife or spatula. It is fibre reinforced to hold its body once applied.
Traditionally used to fix small holes and cracks in tanks or on roofs etc.
Not the highest UV resistance but will last for many years outside in the sun.
BlakSeal
Slightly thinner than BlakJak to enable brush application and still fibre reinforced. Used to patch metal flashing, malthoid waterproofing or as a general gap filler.
This grade is perfect for use as a cost effective waterproofing membrane for retaining walls and the like. Always apply on the dirt side of the wall so that any water pressure ‘pushes’ the material onto the wall.
This product was commonly known as underbody filler for use on cars, trucks and boats.
UV resistance is similar to that of BlakJak.
BlakPaint
Thin bitumen cut-back without fibre reinforcing to be applied by brush or roller.
Used as a ‘primer’ for further bitumen compounds or malthoid on concrete or metal. Can be used to seal porous substrates such as concrete tanks and pipes etc.
UV resistance is slightly less than the above, mainly because of its lower build thickness per coat.
SilvaSeal
Much the same as BlakPaint but the material is filled with aluminium powder to provide additional UV resistance and lower absorbed heat. Contains no fibre reinforcement.
Used to protect metal surfaces, including old metal roofs, tanks, pipes etc. Also used as a finish coat over exterior bituminous waterproofing as it protects black bitumen from the sun, increasing longevity.
Highest UV resistance and protection of the range.
For further information or application specific advice please contact our friendly and helpful sales staff.
https://tarpits.org/experience-tar-pits/excavations
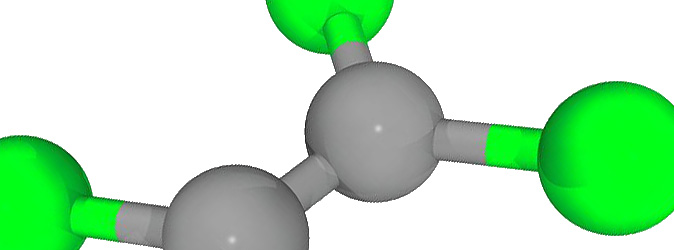
Volatile Organic Compounds
February 2, 2021
So what are VOC’s and why are they so important?
Volatile organic compounds (VOC’s) are potentially hazardous vapours emitted from certain solids and liquids at relatively low temperatures. Many common household items can contain VOC’s and the chemicals emitted can have both short and long term adverse effects on your health.
United States EPA studies have shown that concentrations of about a dozen common organic pollutants, also known as VOC’s, can be 2 to 5 times higher inside homes than in the outdoors. This is regardless of whether the homes were located in rural or highly industrial areas.
Common sources of VOC’s include:
- Paints, strippers and solvents
- Wood preservatives
- Aerosol sprays
- Cleansers and disinfectants
- Air fresheners
- Fuels and automotive products
- Hobby supplies
- Dry-cleaned clothing
- Pesticides
- Building materials including adhesives, sealants, chip board, vinyl flooring and carpet
- Home furnishings
- Office equipment and supplies
How can VOCs impact your wellbeing?
There are many identified health risks associated with VOC exposure:
- Eye, nose and throat irritation
- Headaches, loss of coordination and nausea
- Damage to liver, kidney and central nervous system
- Some organic compounds are suspected or known to cause cancer in humans
Some key exposure symptoms include:
- Headache
- Allergic skin reaction
- Shortness of breath
- Reduced cholinesterase levels
- Nausea
- Vomiting
- Nose bleeds
- Fatigue
- Dizziness
How can I help reduce VOC exposure and their effects on health and the environment?
There are many positive and intentional steps individuals can take to make change and better protect themselves from exposure.
- Make sure work areas are well ventilated.
- Only buy products in quantities that you will use quickly and don’t store opened containers when possible.
- Dispose of unused or little used containers according to directions.
- Don’t store chemicals or fuel containers within inhabited areas.
- Read, understand and follow the manufacturer’s instructions for products before starting.
- Consider which products you use and choose no or low VOC alternatives if available.
Adjuvate Australia have a long standing commitment to community health and the betterment of the environment. Our hand picked technical team have over 40years in the industry and are actively involved in formulating to minimise emissions from our superior range of building products.
Contact our sales team, they are more than happy to discuss the calculated VOC levels of our products and assist with the selection of the best building materials for your application.
Source https://www.epa.gov
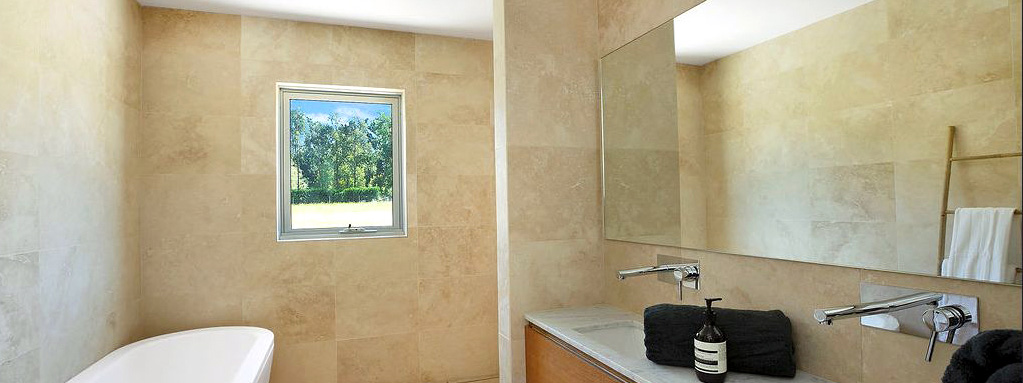
Flooring Adhesives from Adjuvate
January 2, 2021
Adjuvate Australia are, the industry trusted supplier, when it comes to application specific custom tile and building adhesives. Bespoke formulations are designed and produced for new construction, renovations, or even practical or aesthetic upgrades. Adjuvate products are manufactured in Australia and tested to the most stringent Australian Building standards. A comprehensive range is available under licence to 3rd party customers or under the Adjuvate brand throughout the Pacific Islands.
A sample of the Adjuvate premium adhesive range to consider for your next project;
- Adjuvate 1000 – A low-odour, trowel-applied, water-based resin rubber adhesive designed to adhere reinforced vinyl tile, mineral fibre backed sheet vinyl, natural cork tiles, and select secondary backed carpets to smooth, clean, and dry porous subfloors.
- Adjuvate 3300– A non-hazardous, trowel-applied, water-based acrylic co-polymer adhesive that bonds vinyl floor, wall coverings, and PVC backed carpets.
- Adjuvate 8400 – An antimicrobial, pressure-sensitive adhesive with high resistance to concrete surfaces with high alkalinity.
- Adjuvate Neoprene – A contact adhesive used for bonding leather, rubber, and other shoe materials. It is also found beneficial for adhering flooring and tabletop materials like vinyl, linoleum, or cork to substrates like wood, fibreboard, masonite, and more.
- Adjuvate Econogrip – A general purpose, cement based, water resistant adhesive for adhering most types of ceramic tiles, stone and slate to rigid surfaces such as concrete, cement render, brickwork in wall and floor applications.
- Adjuvate OnePot Grip – A ready to use white synthetic resin based adhesive designed for laying mosaic and ceramic tiles onto fibre cement, plaster, gyprock or masonry walls in interior applications.
- Adjuvate UltraGrip – A cement based, rubber modified, highly deformable ceramic tile adhesive designed to bond ceramic and stone tile to concrete, cement render, block work, plasterboard and fibre cement substrates.
Contact our friendly Adjuvate team to learn more about their quality adhesives.
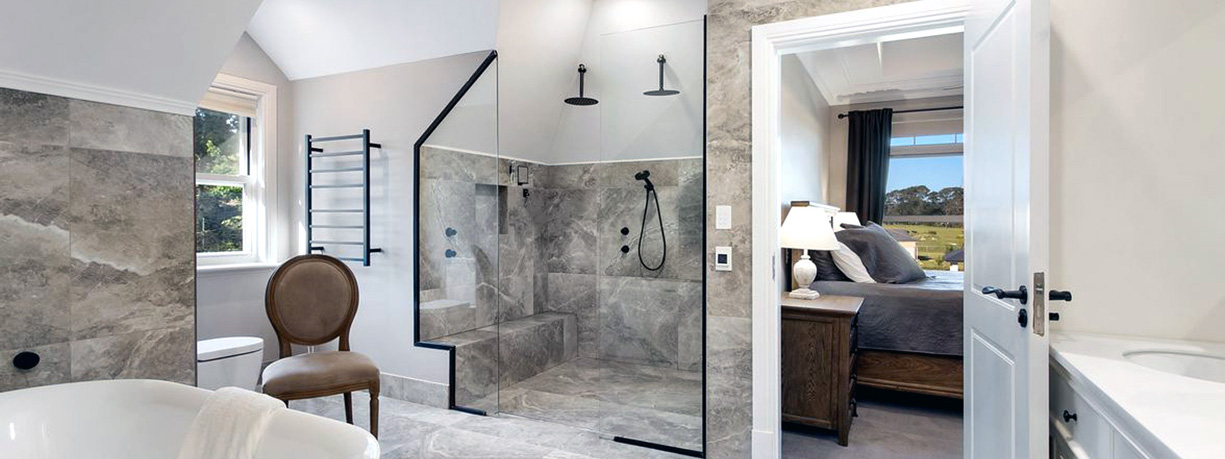
Adjuvate Australia – Website launch…
December 1, 2020
Adjuvate Australia, a name synonymous with premium construction chemical solutions throughout the Pacific region has just launched our new and updated website. Backed by nearly three decades of direct industry experience, we are the trusted partner for many in the custom design and manufacture of construction chemicals, adhesives, sealants, coatings, and waterproofing solutions for civil, commercial and residential projects.
Adjuvate is proud to provide local consulting, design, manufacturing and extensive testing capabilities from our base in the Southern Highlands of New South Wales. Engineering local solutions for numerous global “brand names”, all Adjuvate Australia products are formulated and tested to conform to relevant Australian Standards. Aside from our manufacturing expertise we have grown to be the “go to” supplier of difficult to source products and chemicals for our customers.
Our manufactured range includes;
- Ceramic tile underlay, adhesives and grouts.
- Adhesives for Vinyl, carpet, woodworking, hobby and general construction.
- Waterproofing coatings, damp-proof course, mastics, membranes, and repellents.
- Concrete additives, curing compounds, sealants, and resurfacing products.
- Cementitous coatings, renders, mortars and GRC compounds.
- Specialised construction grouts and shotcrete.
For more information or assistance with bespoke construction solutions by Adjuvate please contact us today.